Polyurethane grouting involves injecting expanding polyurethane to fill and seal cracks, voids, and re-level slabs.
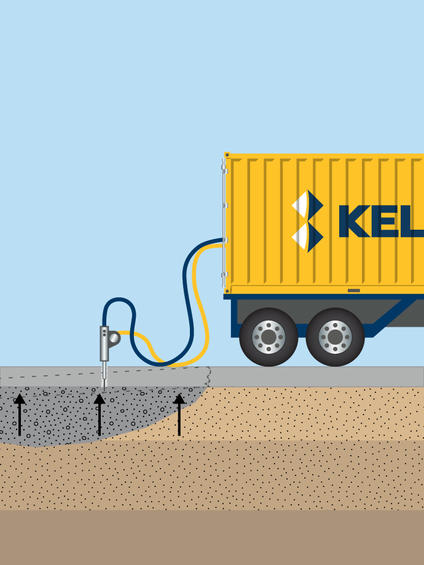
Common uses
Process
Polyurethane grout comes in two forms, single component, and plural component. Many polyurethane grout techniques are available with variations in density, reaction time, reaction with water, expansion characteristic, and flexibility of the reacted grout. It is essential to select the correct grout for each application.
HB PolyLift® Polyurethane Injection is a releveling technique that raises concrete slabs and fills voids using the regulated injection of lightweight, non-hazardous expanding polyurethane grout. When ground improvement is needed along with releveling, compaction grouting is performed first to densify deeper loose zones. Then holes are drilled through the concrete slab or foundation for polyurethane grout to be injected to fill the remaining voids and complete the lifting to the final grade. After releveling, the drill holes are cleaned and filled with cement grout. The result is a densified subgrade, filled voids, and a releveled and stabilized concrete slab.
These grouts have a very low viscosity and can be injected into loose sandy soils and react with groundwater. Additional catalysts can be added to speed up reaction times for these grouts. These grouts are typically used to seal leaking cracks in subterranean concrete pipes, walls, tunnels, and culverts. They are also commonly used to stabilize loose sandy soils by injecting into the wet soils to varying depths either to stabilize them or for curtain grouting to stop underground water migration.
These grouts are used to fill large voids and to relevel concrete slabs. These grouts are installed using proportioning equipment that heats the chemicals and pumps them through a series of hoses that attach to an impingement gun that mixes the chemicals at a 1:1 ratio. As the chemicals mix, a chemical reaction begins, creating a polyurethane foam that expands at varying rates based on the formula. These grouts range in density from 2 pcf to 12 pcf and expand, exerting approximately ten psi of pressure, enough to move a concrete slab.