Vibro compaction is a ground improvement technique that densifies clean, cohesionless granular soils with a downhole vibrator. It is a technique first developed by Keller in the 1930s that has been used on thousands of projects since.
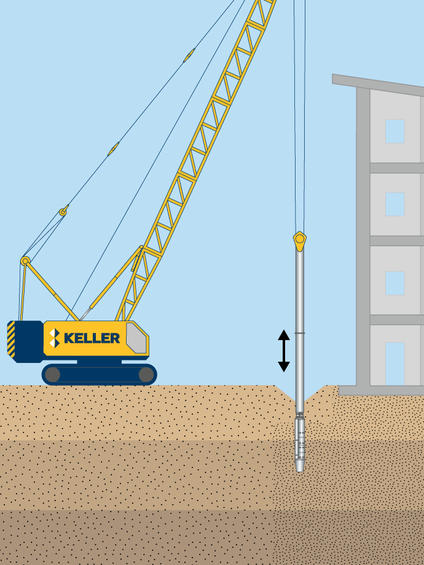
Common uses
Process
The vibrator is typically hung from a crane and lowered vertically into the soil under its weight and vibrations. Penetration is usually helped by water jets integrated into the vibrator assembly. After reaching the bottom of the treatment zone, the soils are densified as the vibrator is raised in lifts. During vibro compaction, clean sand backfill is typically added at the ground surface to compensate for decreased soil volume from the densification process. The vibratory energy reduces the intergranular forces between the soil particles, allowing them to move into a denser configuration, typically reaching a relative density of 70 to 85%. The treated soils have increased density, friction angle, and stiffness. Compaction is achieved above and below the water table.
The improved soil characteristics depend on the soil type and gradation, the spacing of the penetration points, and the time spent performing the compaction. Generally, the vibro compaction penetration spacing is between 6 feet and 14 feet, with centers arranged on a triangular or square pattern. Compaction occurs without stresses in the soil exceeding the overburden stress, ensuring permanent densification.
Using clean sand backfill during vibro compaction maintains the original site elevation to be maintained. However, on sites where the planned final grade is below the existing grade, no backfill is added, resulting in lower site surface elevation during compaction., typically
Vibro compaction allows economic spread footings with acceptable settlements and design bearing pressures generally in the range of 5 ksf up to 10 ksf. The process also reduces the seismic liquefaction potential. The required treatment depth is designed for each project, typically 15 to 50 feet, with a maximum depth of 120 feet.
Vibro compaction rigs can be fully instrumented with an onboard data acquisition system. Data from the system, such as amperage and lift rate, are recorded and displayed in real time alongside specified target values on an in-cab monitor. Monitoring allows the operator to correct any deviations in real-time during the construction process to keep the vibro compaction within project specifications.
Advantages
Quality assurance
The vibro equipment we use is designed and manufactured by our in-house equipment manufacturer exclusively for use by Keller companies.
In-house quality production manager software enables us to capture and analyze data in real-time and validates the ground improvement performance. Various production parameters are generally logged during execution, including depth, current, pull-down force, uplift/pull-down sequence, time and date, and element number. Field trials can verify column production parameters, static load tests, single or group column material compressive strength tests, and column diameter verification.