Rigid inclusions (RIs) are high modulus/controlled stiffness grout columns typically installed through weak, highly compressible soils to reduce settlement and increase bearing capacity.
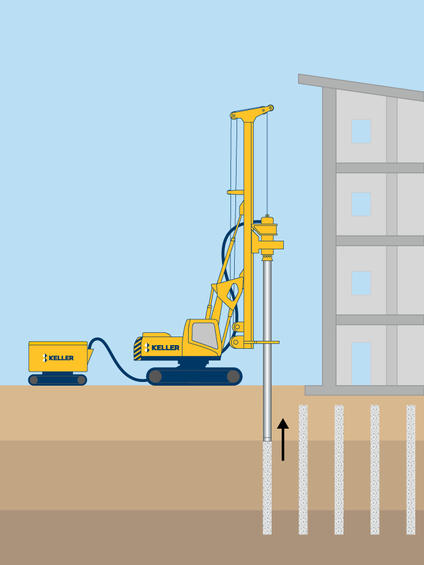
Common uses
Process
After the working platform is prepared, the rig is placed, and data recording starts. A bottom-feed mandrel with a top-mounted vibrator is advanced through the weak strata to the underlying firm stratum. Granular-bearing soils experience some densification due to displacement. Concrete or grout is then pumped through the mandrel. The mandrel may be raised and lowered several times within the bearing depth to construct an expanded base (if required by the design).
The mandrel is then extracted while a positive concrete head is maintained. The concrete fills the void created by the mandrel during extraction. The top of the inclusion typically terminates in a strong stratum or is overlain by an engineered relieving platform. The improved performance is due to the reinforcement of the compressible strata with the high-modulus columns. Ground improvement efficiency depends on the stiffness relationship between the soil and the columns. Load from the structure is distributed to the soil and columns via a load transfer platform or rigid foundation.
Advantages
Quality assurance
Quality control in the field begins with an accurate layout of the rigid inclusions locations. The tool is centered at each staked location within the specified tolerance. For each rigid inclusion, a log is generated providing the following: project information, column identification, diameter, length, start time, end time, penetration depth, pump stroke count, neat grout volume (theoretical), actual grout volume, penetration rate, and crowd pressure or applied torque.
Keller has developed proprietary data acquisition (DAQ) equipment and software for real-time monitoring and recording of all parameters during the rigid inclusion construction process. In-cab monitors display real-time quality control feedback to the operator and field engineer during construction and graphically display data such as grout volume and depth alongside specified target values. The DAQ system transmits all data in near real-time to a central online database via a cell modem. After curing, the grout is regularly sampled and cast into cylinders for strength testing. Load testing of a test rigid inclusion, or group of rigid inclusions, can be performed to verify the design assumptions.