Aragon Properties Ltd. is establishing a new mid-rise development complex in Port Moody, British Columbia called Platform featuring over 100 one to three-bedroom homes, townhomes, and live/work lofts.
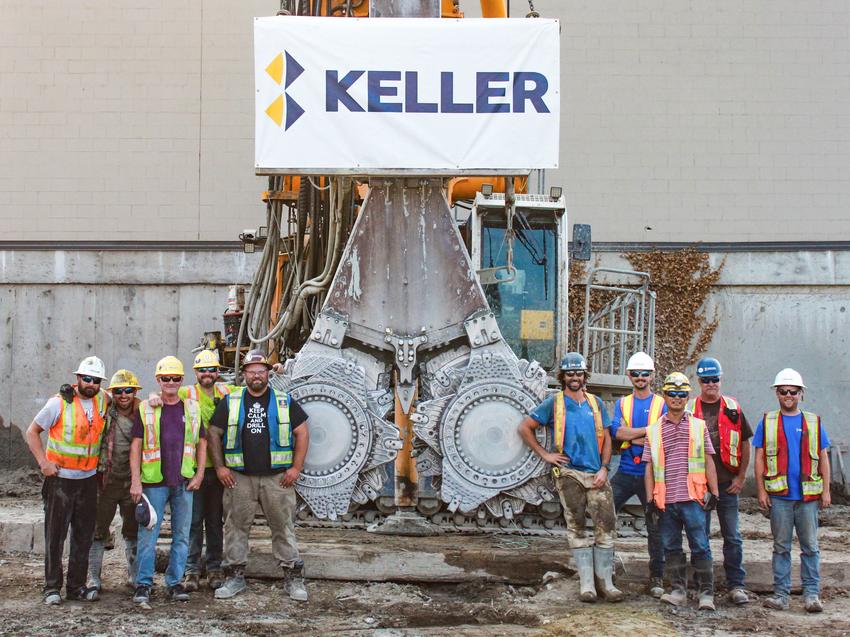
Ameet Johal, Aragon’s Director of Sales and Marketing, says, “There will be retail/commercial spaces at street level, and we’re expecting at least one will be a restaurant or other eatery that will become a gathering place where people can engage with their friends and neighbors.”
Cutter soil mixing (CSM) is well-suited for areas in the lower mainland and Pacific regions of Vancouver with deltaic alluvial flow deposits where there are few obstructions. Developed from diaphragm wall technology, CSM uses two sets of counter-rotating, vertically mounted cutter wheels that cut the surrounding soil and blend the injected cement slurry with the in situ soil to form soil cement panels.
Keller performed earth retention and excavation support at 2718 Clarke Street on the approximately 38-m-tall by 79-m-wide property to aid in the establishment of Aragon’s modern living spaces.
“Working with Keller was a big win for us and we highly recommend them,” said Kris Hellens, EIT, Senior Project Coordinator for Aragon Construction Management Corp. “In addition to the excellent back-end support from their office staff, their site crew consisted of some of the most helpful, cooperative, and responsive people I’ve had the pleasure of working with. Keller’s whole team was able to react on the fly to changes in the plan without any issues and provided constructive insights on how to get the best possible product.”
The CSM shoring wall was designed as a temporary earth retention structure anchored to support the maximum excavation depth of almost 11 m and embedded in a silt layer to restrict seepage of groundwater into the excavation pit. Field Engineer Johannes Reinisch explains that construction included the supply and installation of almost ninety 650-mm-thick CSM panels to a depth of up to nearly 16 m.
“The significance of CSM technology lies in its efficiency and consistency,” says Assistant Project Manager Anand Mitchell. “Had Keller approached this project with an alternative technique, it would have taken three times as long. The cutter tool takes about two hours doing the work of three drill rigs to create the panels/walls in the ground.”
The main challenge was installing the panels in tight corners close to an adjacent building on the west side of the property and ensuring verticality to avoid intrusion into the planned excavation pit.
“Reaching the planned production rate required skilled workmanship to ensure safe completion on schedule,” he continues. “Site logistics, safety protocols, and production sequences needed to be thoroughly planned, reviewed, and executed on each work shift.” Due to limited storage space on site, delivery of cement and H-piles was timed to coincide with the construction schedule.
Keller then completed the installation of 124 H-piles within the CSM panels. Superintendent Bradley McKay was pleased to report that production finished one week ahead of schedule due to Keller exceeding production targets.
Kris continued, “Keller’s innovative materials testing solutions allowed us to meet the requirements of our consultants without sacrificing schedule, and their precision drilling saved us valuable square footage within the site. The soil mixing method proved to be fast, efficient, and minimally disruptive, resulting in no complaints from the neighbors and saving Aragon from having to perform repairs to the adjacent properties.”
Keller will return to install two levels of anchors for a separate scope of work, which is anticipated to last a couple of weeks.