Keller has successfully completed work on what’s believed to be the largest permanent soil nail wall ever constructed in the United States. This technically challenging project now allows for the construction of a new stadium for Major League Baseball’s Texas Rangers.
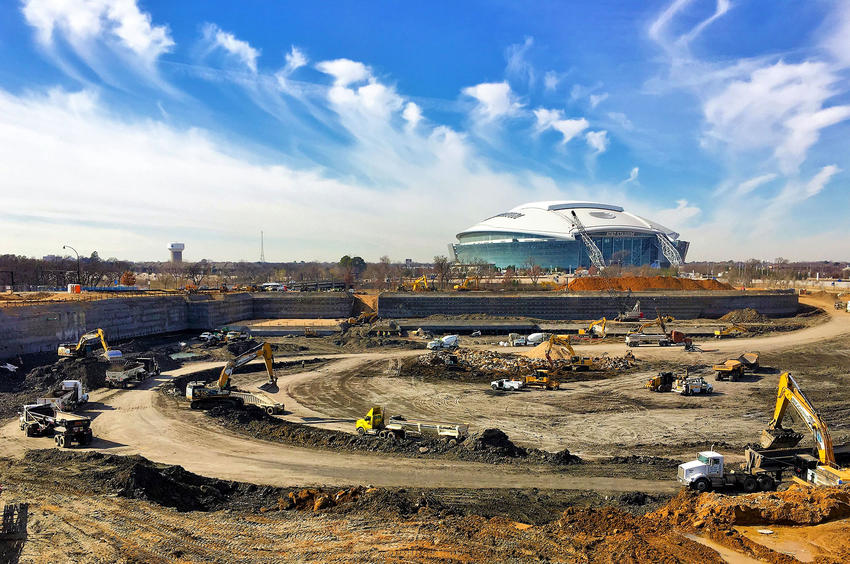
The permanent retention system is over 4,000ft (1.2km) long and covers more than 250,000ft² (23,000m²). It surrounds what will be known as Globe Life Field, which will open to fans at the start of the 2020 season.
Having successfully carried out similar works for the nearby and similarly high-profile Dallas Cowboys’ gigantic AT&T Stadium 12 years ago, Keller was approached by construction contractor Manhattan and the project’s design team early in the planning stage.
“There have been a lot of improvements in equipment and processes since we worked on the Cowboys’ stadium, and these combined with our previous experiences and good relationship with Manhattan meant we were able to successfully win the contract,” explains Marty Schrantz, Keller Branch Manager.
Big challenges ahead
Whereas the AT&T project was relatively straightforward, this project required another 100,000ft² of wall and threw up a number of other significant challenges.
Firstly the ground, composed of clays, sandstone, and shales, contained many fractures, joints, and weak planes that had to be accounted for. Also, randomly scattered throughout the site were dense, irregularly shaped boulders of hard, limy sandstone, which required partial removal. This had to be done with special care so as not to cause cavities, which would have been problematic for the shotcrete facing.
Secondly, the retaining wall had to follow a line with numerous juts and corners. “For the latter, we introduced an alternate hybrid anchored drill shaft system,” explains Joel Clark, Keller Senior Engineer.
“This was initially developed on the AT&T project and alleviated the soil nail congestion and crossover at either side of the corners while providing the resisting forces needed to retain the inherently unstable wedges of ground at these points.”
Bringing in the drilling experts
An anchor drilled system was also required in some places due to utility services for an adjacent entertainment complex under construction. Keller also undertook this work as well.
“The schedule was very tight and this was a large project, requiring multiple rigs and a lot of coordination with other trades,” says Austin Pruitt, Assistant District Manager. “We had to be flexible to meet the changing daily demands and the boulders were challenging. If we hit one, we’d put a core barrel on and drill through it if we could. If not we’d dig it up. We also had to use temporary casing because of the sandy soils. It was hard work but it all went well thanks to brilliant coordination and a great team effort all round.”
Advances in construction methods since the team worked on the AT&T Stadium now make soil nailing faster, safer, and more efficient than ever. There were other efficiencies, too. For example, for the Cowboys’ stadium, sacks of grout materials were broken up manually and dumped into the mixer at a rate of up to 3,000 sacks per day; on this project, materials were handled in bulk using silos and high-speed mixers.
Similarly, the team was able to site-batch the shotcrete to ensure a continuous operation and allow work to take place at weekends or immediately after bad weather. A typical ready-mix plant wouldn't have had the materials readily available.
Monitoring technology
There were advances when it came to monitoring as well. Historically, a wall of this size would require extensive resources and ongoing efforts to monitor deflection at critical sections during construction. However, fellow Keller company Geo-Instruments was able to provide a comprehensive and technologically advanced monitoring program that saved time, increased accuracy, and minimized field effort.
This included three automated motorized total stations and four automated vertical inclinometers to provide continuous, real-time monitoring. Once installed, they generated data without any additional fieldwork. The monitoring, with alarms set at predetermined thresholds, provided assurance that actual deflections remained in line with those predicted in the design.
“This project was another example of us working together within the Keller family to provide the client with an integrated approach right from the start,” says Paul Thurlow, Geo-Instruments Vice-President. “Apart from the obvious safety and design verification aspect, the back analysis of data and its potential to improve designs in the future will keep Keller ahead of the game. It was an immense project, technically challenging and fast track from start to finish, but working with the Keller site team and design staff was a real pleasure for all of us.”
His words are echoed by Marty Schrantz: “We had a great team out here and everyone in the lineup did their part to make this project a real success.”