Logan International Airport, owned and operated by the Massachusetts Port Authority (Massport), is one of the busiest airports in the northeastern United States, with annual passenger travel volume projected to increase by about 18% by 2024. This increase will inevitably translate to a comparable traffic increase along the already congested airport vehicle routes.
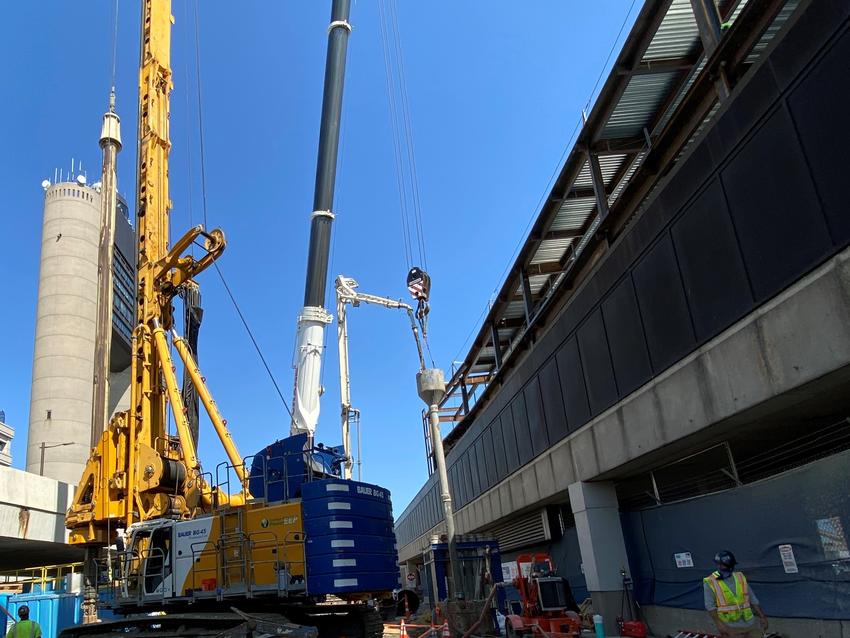
The project
As part of Massport’s 4-year Capital Program, a multi-billion-dollar upgrade initiative was launched at Logan, which included the construction of a new elevated roadway connecting Terminals B and C. The new elevated roadway parallels the existing ground-level terminal connector road and is for the dedicated use of passenger buses and other airport service vehicles. Keller was awarded the foundation package consisting of drilled shafts to support the elevated roadway as well as micropiles to underpin an existing utility tunnel.
The challenge
- Foundations were required to be installed within a relatively narrow, 50-ft-wide corridor with headroom limited to 20-ft in places.
- Installation of full-length (up to 140 ft) cages for the drilled shafts required a complicated two-stage operation.
The solution
Drilled Shafts
Sixty-inch diameter shafts were drilled approximately every 100 ft along the elevated roadway alignment. Shafts excavation was made with polymer drilling fluid and typically extending through overburden and Boston Blue Clay up to 120 ft thick and socketed into underlying competent bedrock. Reinforcing cages were fabricated off-site in two sections and trucked to the work corridor as needed. All cages were fitted with access tubes for Crosshole Sonic Logging (CSL) testing to aid in confirming concrete integrity along the shaft depth.
The first reinforcing section was lowered into the cased drill hole by crane and mechanically suspended above the casing to allow the second section to be spliced. Column connection details were critical. While drilled shafts are typically installed to a 3-inch tolerance, the column steel is limited to a 1-inch tolerance; thus, survey accuracy was paramount and required multiple levels of cross-checking between project teams.
Micropiles
Eight, 9.625-inch diameter micropiles were installed to support an existing utility tunnel. Given the low headroom conditions, structural retrofits, and loading conditions, micropiles were also used as foundation elements elsewhere on the site. Due to certain headroom constraints at existing ramps, one of the drilled shafts was replaced with four micropiles. Retrofits to the existing adjacent elevated roadway include the installation of micropiles to increase loading at existing columns. Despite the challenges, the foundation work package was completed ahead of the project deadline.