In response to significant flooding events and working under an accelerated construction schedule in record-high temperatures, Keller constructs some of the largest drilled shafts in Arizona.
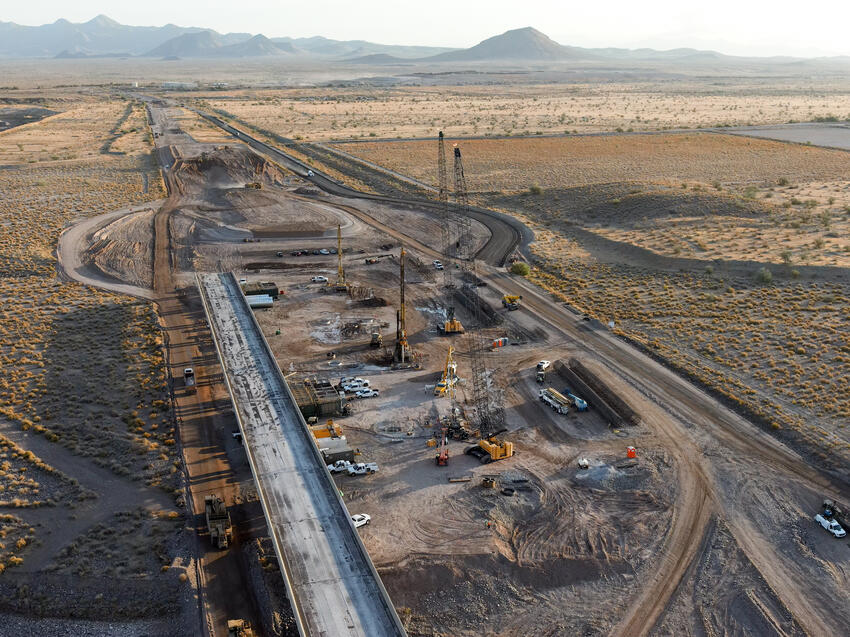
The project
Diverted by dams at its headwaters, the Salt River is primarily dry, except during monsoon season or when excess mountain snowmelt causes significant flooding downstream. The Gilbert Road Bridge, which crosses the Salt River, was constructed in 1990 as a two-lane bridge, managing traffic from the East Valley to Highway 87. With the bridge quickly exceeding its capacity, a low-flow crossing was installed adjacent to it in 2005. However, the crossing was prone to damage during flood events, prompting the decision to construct a replacement four-lane bridge. Ground conditions included loose sandy-silty, gravel material with cobbles through the proposed bridge location.
The challenge
The existing bridge and low-flow crossing were to remain open to traffic during bridge construction. However, during early construction, dam releases caused the river to flood, washing out the low-flow crossing, and the existing bridge and crossing were deemed unrepairable. Therefore, the road was closed, requiring accelerated construction for on-time completion of the new bridge.
The solution
Considering the recent flooding and the threat of future floods, the design engineer emphasized protection from future hydraulic events, requiring some of the largest drilled shafts in Arizona. Keller’s scope included 22 polymer-supported drilled shafts up to 10 ft in diameter, two at each pier and three at the abutments. Shafts were designed to be up to 140 ft long, with concrete terminating 20 ft below the working surface. Close coordination was required to fabricate and install the reinforcing cages on-site, weighing approximately 40 tons each.
Flooding delayed the project's start, so shaft installation began during the challenging summer months when temperatures reached daily high averages of 115 degrees. The concrete required multiple doses of liquid nitrogen to maintain a concrete temperature below 90 degrees during transport and placement. Shift times were adjusted for crew safety, and throughout the project, hydration stations and air-conditioned cool-down rooms were provided to the crews.
Despite the extreme heat and accelerated schedule, Keller completed shaft construction well ahead of the required schedule.