Three tunnels were to be created beneath seven active Amtrak lines serving Boston’s South Station and the financial district.
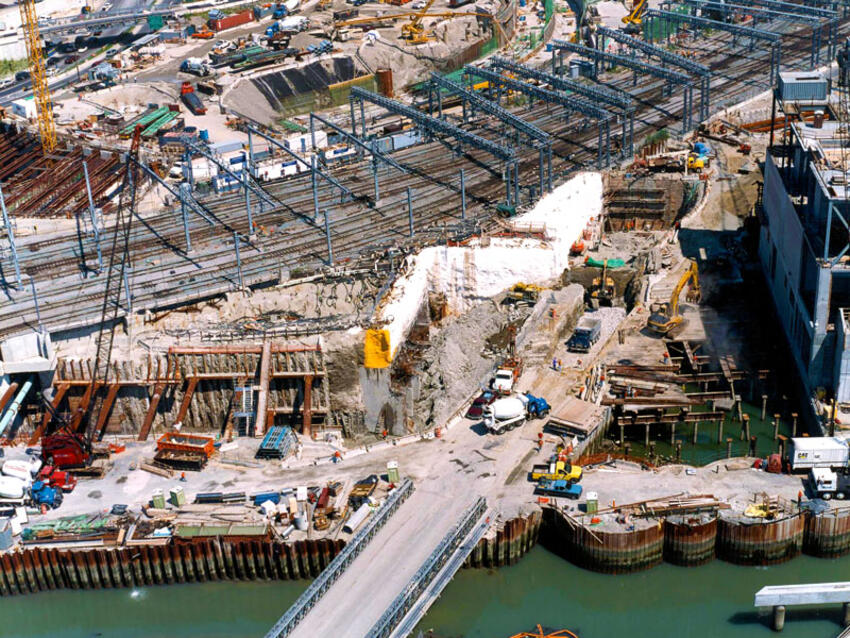
The project
Jacking of three massive tunnels just beneath the seven active Amtrak lines serving Boston’s South Station and the financial district, and through what has been described as “…the most difficult soil conditions imaginable,” is acknowledged as the most demanding component of the overall Central Artery Tunnel project. The jacked tunnel method was selected to allow full rail service to the station during tunnel construction.
The soil profile through which tunneling would occur included 20 ft of historic fill containing building debris, granite seawalls, piles, wharf structures, and abandoned brick structures. This was underlain by soft, organic material and a marine deposit of Boston Blue Clay. Groundwater was encountered approximately 10 ft below the ground surface.
Ground freezing design
Keller designed the ground-freezing program to provide multiple geotechnical functions, including groundwater cut-off, fill debris encapsulation within a frozen ground matrix, and improve organics and marine clay strength along the tunnel alignment.
- A massive, centrally located refrigeration plant
- A brine circulation system capable of pumping 4,000 gallons per minute to any/all of the three jacked box areas
- An insulated brine supply and return manifold system entirely installed within the rail track structure
- Heat pipes to control the lateral growth of frozen ground beyond the box perimeter
- Over 2,000, 4-1/2-inch O.D. steel freeze pipes installed from 46 ft. to 60 ft below ground surface
Accurate spacing and freeze pipe location were critical to the success of the stabilization program. Finite element modeling was performed to determine the transient heat flow from the ground to the freeze pipes and evaluate freeze pipe disposition, freeze formation period, and freeze plant capacity. With most of the excavation work undertaken in the Boston Blue Clay, which also required the greatest refrigeration effort, all design work and detailed thermal analyses were focused on this stratum.
System installation and operation
Freeze pipe installation was accomplished from the rail tracks using sonic drilling techniques. Highly maneuverable, high-rail mounted equipment was utilized to precisely locate the pipes among the complex track switchgear, and the sonic drill head could readily penetrate many obstructions. This was invaluable in allowing the contractor to maintain the required pipe configuration.
Chilled brine was circulated through the freeze pipe system for three to four months before tunnel jacking. The ground freezing contractor also designed a computerized instrumentation system that was installed and remotely monitored to ensure frozen ground conditions before the start of tunneling.
The ground-freezing program provided a stable and predictable, completely unsupported, 80 ft. wide by 40 ft. high vertical face, allowing an open-faced tunnel shield.
The tunnel was jacked in place without incident or disruption to rail service, and ground freezing was estimated to have resulted in a multi-million dollar saving. Ground freezing was used for all three tunnel sections.
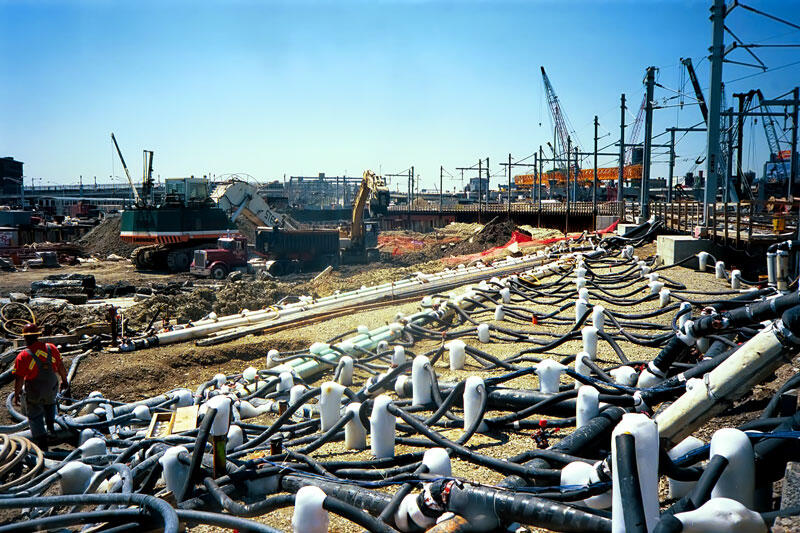