The Trinity River Tunnel is a small but critical portion of the 150-mile-long, $2.3 billion Integrated Pipeline (IPL) tunnel project in Dallas, TX. When the tunnel boring machine (TBM) became mired, Keller’s emergency response capability was key to a speedy resolution.
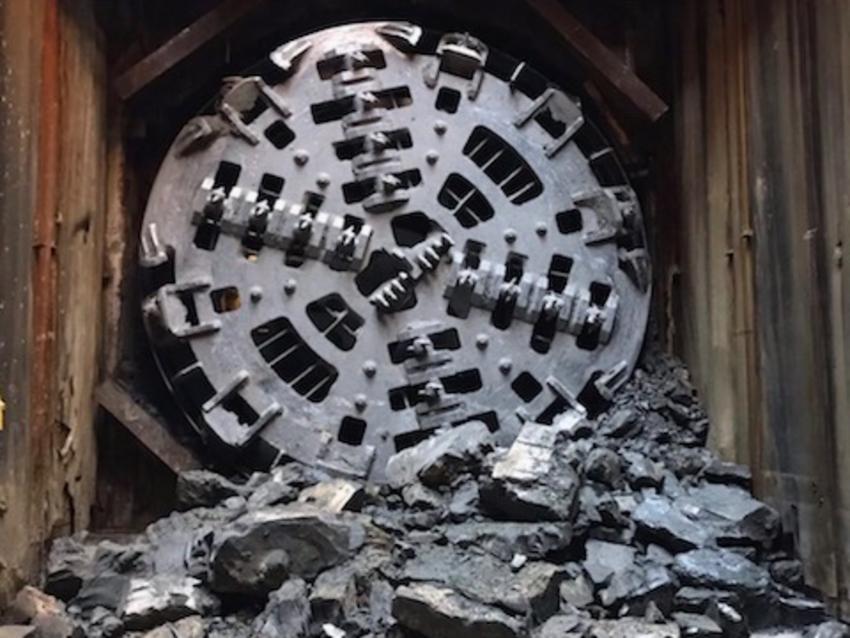
The project
The Integrated Pipeline (IPL) is designed to bring hundreds of millions of gallons of water a day from three East Texas reservoirs to meet increasing demand in North Central Texas. A TBM was required to create a 16-ft diameter tunnel section beneath the Trinity River. The TBM had cleared the underwater portion of the drive and was 50 ft underground and 800 ft from the East exit portal when it encountered a region of highly weathered mudstone. Attempts to advance through the mudstone created a large void in front of and above the TBM, effectively miring it in place.
The challenge
Several challenges needed to be addressed:
- Tunneling projects are linear, one-directional, and schedule-focused. The next phase cannot be initiated until the previous phase has been completed. Time was therefore of the essence.
- The surface area immediately above the TBM was designated wetland. Therefore, any mitigation programs requiring vertical drilling were precluded.
- Surface soils above the TBM included saturated, high plasticity clays several feet thick in places, making drilling conditions very difficult.
The solution
Keller worked with the tunneling contractor to develop an ultrafine cement permeation grouting program to stabilize the soils. Within six days of receiving the contract for the work, Keller had mobilized a crew to the job site. Keller was able to begin the mitigation effort within 10 days of contract execution. To comply with wetland restrictions, Keller’s grouting design called for Tube a Manchette (TAM) pipes to be installed at a 45° angle from an accessible area outside the wetland perimeter. A fan pattern of 80-ft deep TAM pipes was installed for the grouting itself. Fiberglass dowels that could easily be bored through when the TBM resumed tunneling were used to reinforce the weathered mudstone and soils above and in front of the voided zone. During TAM installation, the drill spoils were captured by a vacuum truck and transported off-site.
Pinpoint accuracy for TAM pipe was critical since some pipes were terminated just inches from the TBM. To ensure this, Keller affiliate Geo-Instruments provided a sophisticated gyro measuring system that was mounted on the drill mast and allowed compound angles of the TAM pipe to be achieved. Despite the challenges, the TBM was able to resume tunneling with minimal delay.
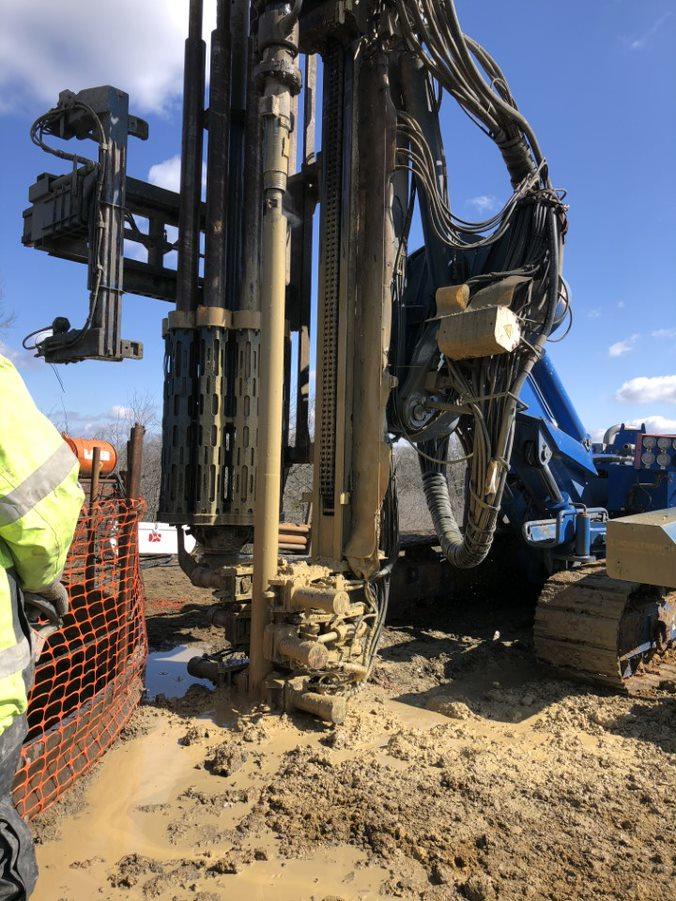